Research on the new energy industry chain: solid-state batteries: solid-state ba
2024-07-23
I. Introduction
Solid-state batteries are considered an ideal solution to address the safety issues of lithium-ion batteries and to enhance energy density, positioning them as the next-generation battery technology with significant industry focus and strategic deployment.
Since 2022, the research and development as well as industrialization of solid-state batteries have made noticeable progress. Domestic companies have significantly exceeded expectations in terms of technological advancements and cost reduction in the field of semi-solid-state batteries.
II. Advantages and Challenges of Solid-State Batteries
The performance of lithium-ion batteries is reaching its upper limit, and the demand for upgrades is driving technological iteration. As the penetration rate of electric vehicles continues to increase, the requirements for battery safety and driving range are becoming more stringent. Liquid lithium-ion batteries, as the mainstream technology route for power batteries, on one hand, have issues such as the flammability and high corrosiveness of organic solvents in the liquid electrolyte, and the inevitable lithium dendrite problems during charging and discharging processes, which raise concerns about battery safety. On the other hand, the energy density of liquid batteries is approaching the ceiling constrained by the material system, limiting the room for upward iteration. In the current stage where homogenized overcapacity is severe, breaking away from cost orientation and exploring new technologies to seek breakthroughs in safety and performance has become a new evolutionary path for the power battery industry.
Advertisement
Solid-state batteries may be the most promising direction for battery technology development at present.
Based on the mass percentage content of liquid electrolyte in the battery, lithium batteries can be classified into liquid batteries, semi-solid-state batteries, quasi-solid-state batteries, and all-solid-state batteries, with the latter three collectively referred to as solid-state batteries. Solid-state batteries follow the same charging and discharging principles as liquid batteries and replace the liquid electrolyte and separator in liquid batteries with a solid electrolyte, eliminating the safety hazards of flammable leaks. At the same time, they significantly enhance the energy density of the battery, making them a key research direction in academia and industry.
Advantages: High Safety and High Energy DensitySolid-state batteries can fundamentally address the main safety hazards of lithium-ion batteries. Traditional lithium-ion batteries may experience safety incidents such as spontaneous combustion and explosions, which originate from the flammable and volatile organic electrolyte. Overcharging and internal short circuits can lead to thermal runaway, igniting the electrolyte at high temperatures, ultimately causing the battery to catch fire or explode. Moreover, the corrosion, evaporation, and leakage of the electrolyte can also pose serious safety risks to the battery system. In contrast, solid-state electrolytes are inherently non-flammable,耐高温, non-corrosive, and non-volatile, with mechanical strength, thermal stability, and electrochemical stability that surpass those of traditional electrolytes, thereby fundamentally enhancing the safety level of the battery.
The material system and battery structure are comprehensively optimized, resulting in a significant increase in energy density.
Improving energy density is one of the primary goals of battery technology evolution, mainly achieved through two approaches: 1) using cathode and anode materials with higher capacity and greater potential difference; 2) increasing the proportion of active materials in the battery. In liquid lithium-ion batteries, the first approach mainly corresponds to the application of high-performance materials such as high-nickel ternary and silicon-carbon anodes, but the voltage window of the electrolyte directly limits the range of available cathode materials. The second approach can be realized by improving battery packaging processes, reducing the thickness of current collectors, and increasing battery size. However, with the rapid development of the industry, the marginal effects of packaging optimization and current collector weight reduction have become minimal, and the continuous increase in battery size is constrained by issues such as thermal management. Solid-state batteries, on the other hand, break through the various limitations faced by traditional lithium-ion batteries, thereby achieving a leap in energy density:
Solid-state batteries can accommodate high-voltage cathode materials.
Compared to traditional electrolytes, the electrochemical window of solid-state electrolytes is increased to 5V, and it is more compatible with material systems that have severe interfacial reactions in liquid batteries, such as high-nickel cathodes, manganese-containing compounds with manganese dissolution issues, and high-voltage cathode materials, opening up the energy density ceiling.
The excellent mechanical properties of solid-state electrolytes make the use of lithium metal anodes possible.
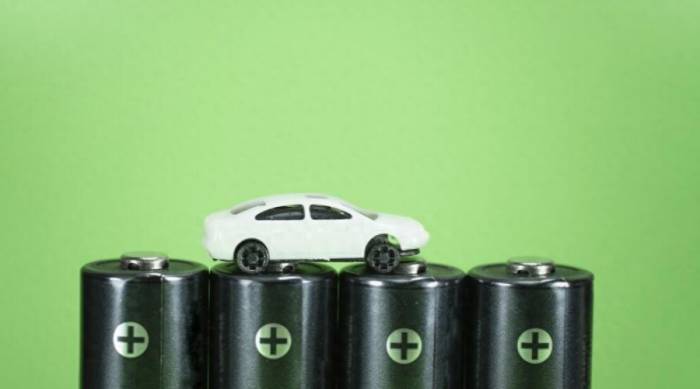
Lithium metal, as an anode, has a theoretical capacity of 3860 mAh/g, about 10 times that of graphite, making it the most ideal anode form in terms of capacity. However, lithium metal has poor stability, and traditional liquid lithium batteries that use metallic lithium anodes can produce lithium dendrites that pierce the separator during the cycling process, leading to internal short circuits, affecting safety and cycle stability. Solid-state electrolytes, with their excellent mechanical properties, can effectively suppress the formation of lithium dendrites, are compatible with lithium metal anodes, and can achieve a leap in energy density.
Pack design is simplified, and system weight is reduced.
Solid-state electrolytes combine the functions of electrolytes and separators, and if combined with the use of lithium metal anodes, they can significantly reduce the distance between electrodes; individual battery cells can be stacked in series and densely packed to achieve a voltage-boosting effect, thereby improving manufacturing efficiency, reducing packaging size, and increasing volumetric energy density. In addition, due to the excellent heat resistance of solid-state electrolytes, the demand for thermal management in solid-state batteries is reduced, further reducing system weight.
Challenges: Production costs are still high, and technical difficulties remain.The solid-solid interface issue is a pain point in industrialization, affecting the rate and cycle performance. The function of the electrolyte is to build a channel for the transport of lithium ions between the cathode and anode, and the indicator that determines the smoothness of lithium ion transport is called ionic conductivity. At the electrode-electrolyte interface, the traditional liquid electrolyte contacts the cathode and anode in a liquid-solid contact, with good wettability and no significant resistance between the interfaces. However, solid-state electrolytes contact the cathode and anode in a solid-solid interface, with a smaller contact area and poorer tightness, and the ionic conductivity is typically two orders of magnitude lower than that of liquid electrolytes. This characteristic leads to limited fast-charging performance of the battery. Since the solid-solid interface is a rigid contact, it is more sensitive to volume changes in electrode materials, and stress accumulation during charging and discharging can also lead to a decline in electrochemical performance, affecting the cycle stability of the battery. How to balance conductivity, reduce side reactions, and lower impedance remains a direction that the industry is still striving to conquer.
The industry chain is still immature, and costs are high.
Solid-state battery systems typically use high-performance cathode and anode materials, which have not yet truly achieved large-scale commercial use, and their prices are higher than traditional electrode materials. The core material, solid-state electrolyte, has an unclear technological route, and the production process is more complex, involving some high-priced rare metals, making the raw material cost far higher than that of liquid batteries. In terms of manufacturing, the development of mass production processes is even more behind the material system, and some electrolyte systems have strict requirements for the production environment, further increasing manufacturing costs.
III. Solid-state battery materials and processes
Three major routes of solid-state electrolytes are given key layout.
The design and development of solid-state electrolytes are key to the development of solid-state battery technology. The ideal electrolyte material should have high ionic conductivity (>10^-3 S/cm), a wide electrochemical window, and good chemical and mechanical stability for both cathode and anode materials. The mainstream solid-state electrolyte routes are mainly divided into polymers, oxides, and sulfides, each with its own advantages and disadvantages, and the technological route has not yet been determined. The sulfide system is more chosen by Japanese and Korean companies, such as Toyota leading the mass production of sulfide all-solid-state batteries, while domestic and European and American companies mostly tend to choose the oxide electrolyte route.
Oxides have moderate conductivity and good stability, favored by domestic companies.
The ionic conductivity of oxide electrolytes is generally between 10^-6 and 10^-3 S/cm, and their dense morphology gives them higher mechanical strength, good stability in air, and tolerance to high voltages. The main challenge they face is their poor deformability and flexibility, requiring high-temperature sintering. Oxide solid-state electrolytes can be divided into crystalline and amorphous electrolytes according to their form. Crystalline oxide electrolytes have high air and thermal stability, making them easy to produce on a large scale. The more widely studied crystalline solid-state electrolytes include garnet-type LLZO electrolytes, perovskite-type LLTO electrolytes, and NASICON-type LAGP and LATP electrolytes. Among them, LLZO has high ionic conductivity and is stable against lithium metal. Although the high sintering temperature brings higher costs, we believe it has relatively greater application potential in the long term. Amorphous solid-state electrolytes are mainly LiPON-type solid-state electrolytes, with low ionic conductivity, suitable for thin-film batteries, and thus have more application prospects in electronic devices with lower capacity requirements.Sulfide ion conductivity is the highest, but poor stability limits practical application.
Sulfide solid-state electrolytes have garnered widespread attention due to their extremely high lithium-ion conductivity (10^-4 to 10^-2 S/cm), such as LGPS and LSP-SC, whose ionic conductivity at room temperature is comparable to that of traditional liquid electrolytes. However, they have defects in chemical and environmental stability, reacting easily with water to produce toxic H2S gas, making their development the most challenging, with stringent production environment requirements and high mass production costs. Among the different types of sulfide solid-state electrolytes, amorphous LPS and crystalline LGPS, LPSCl, etc., have attracted more attention. Among them, LGPS has the highest ionic conductivity, but the raw material cost is high due to the presence of the precious metal germanium; LPSCl's ionic conductivity can also reach the level of 10^-2 S/cm, and it does not contain precious metals, thus it is more cost-competitive.
Polymers were the first to achieve commercial application, but low room temperature conductivity limits development space.
Polymer solid-state electrolytes are composed of a polymer matrix (such as polyesters, polyethers, and polyamines, etc.) and lithium salts (such as LiClO4, LiAsF6, LiPF6, etc.). The main advantages of polymer solid-state electrolytes are their high flexibility and processability, which means they are already capable of low-cost mass production. However, the ionic conductivity of polymer electrolytes at room temperature is low, only 10^-8 to 10^-6 S/cm, and they need to be heated to above about 60°C to reach 10^-4 S/cm. Research around polymers mainly focuses on improving their conductivity and thermal stability through chemical modification or composite materials.
Cathode and anode: Breaking through limitations, performance boundaries are expanded
The selection range of electrode materials for solid-state batteries is broader, and high-performance is becoming a trend. Solid-state lithium-ion can continue to use the material system of traditional liquid lithium-ion batteries, such as ternary/lithium iron phosphate cathodes, graphite/silicon-carbon anodes. Replacing liquid electrolyte with solid-state electrolyte can greatly suppress the interface reaction of the electrodes, and there is no longer a voltage window limit for the electrolyte, thus the material performance boundaries of the cathode and anode are greatly expanded.
Cathode can continue to use high-nickel ternary, manganese-based, high-voltage materials are expected to achieve breakthroughs.
Among the cathode materials with mass production capabilities, high-nickel ternary cathodes have the largest specific capacity, which is most in line with the high energy density performance goals of solid-state batteries. In the long term, lithium-rich manganese-based, high-voltage cathode materials also have a good application prospect in the solid-state battery system. Lithium-rich manganese-based has a high specific capacity (250~400mAh/g), high operating voltage, and low cost, but still needs to solve problems such as poor cycle and rate performance, low first-week coulomb efficiency, and gas evolution and oxygen release at high temperatures.
After breaking through the 4.5V voltage window, the use of high-voltage cathode materials such as spinel-type lithium nickel manganese oxide and olivine-type LiMPO4 also becomes possible. The working voltage platform of lithium nickel manganese oxide material is as high as 4.7V, which is a significant increase compared to the 3.7V of ternary materials; the open-circuit voltage of olivine-type LiMPO4 material is related to the transition metal, and when the transition metal is Mn/Co/Ni, the voltage can reach 4.1V/4.8V/5.1V respectively.
Silicon-based materials are an important iteration direction for anodes, and lithium metal anodes may be the long-term goal.Silicon's theoretical specific capacity is more than 10 times that of graphite, but it suffers from serious volume expansion, continuous reaction with the electrolyte leading to capacity decay, and poor rate performance. Silicon-carbon and silicon-oxygen materials can suppress volume expansion to a certain extent and improve electrochemical stability, and have been widely used in the anodes of high-energy-density batteries, possessing a certain degree of commercial maturity, and are also suitable for solid-state battery systems. Lithium metal is an even more ideal anode solution, but its extremely high chemical reactivity still poses significant challenges to its industrial application. Different types of solid electrolyte materials have different interface issues with the lithium metal anode, requiring customized solutions. A large amount of research has been conducted around interface side reactions and lithium dendrite issues. How to solve the interface problems of lithium anodes and adapt to the needs of large-scale production remains a challenging topic.
Manufacturing Process: Partial Compatibility, Long-term Cost Reduction Requires Innovation
The wet process has a high overlap with liquid batteries, but the process is cumbersome and costly. In the first step of slurry mixing, since both sulfide and oxide electrolytes will react with water, water-based processes cannot be used, and only organic solvents can be used. However, the drying and recovery of solvents consume a lot of energy, which will significantly increase manufacturing costs. In the second step of coating, although the process is relatively mature, the large-scale production of solid electrolyte thin films still needs to be verified. The third step requires densification of the electrolyte layer to ensure good contact with the electrode, for which calendering/rolling processes can be used for sulfide electrolytes, while oxide electrolytes have poor ductility and can only be sintered at high temperatures, but the temperature must not exceed 1000°C, otherwise it will lead to side reactions and decomposition of the cathode materials.
Dry process has cost reduction potential, and large-scale application still needs to be studied.
In order to improve production efficiency and reduce costs, solid-state batteries may tend to adopt solvent-free dry electrode technology. Dry electrode technology includes homogeneous mechanical dry mixing of active materials, binders, and conductive agents, and dry coating processes. The "powder-film" route can simplify the manufacturing process, eliminate side reactions caused by organic solvents, and also reduce the amount of binder used, increasing the utilization rate of active materials. In the industry, only Tesla claims to have applied dry graphite anode to 4680 cells, and it has not been mass-produced; other companies' dry electrodes are mostly in the stage of process equipment development.
Stacking is the ideal structure for solid-state batteries, and pouch/square packaging has more advantages.
Due to the poor flexibility of inorganic solid electrolyte films, both square and round coil structures will lead to gaps at the material interfaces, which are difficult to compensate for and heal without the electrolyte. Therefore, stacking is the most ideal battery structure for solid-state batteries, where the electrode and electrolyte film are in complete uniform contact, expanding and contracting synchronously and in parallel to maintain good interface performance. The packaging method adopts pouch/square, which can retain the integrity of the cell structure to the greatest extent when entering the shell. In addition, the pain points of gas expansion and leakage in liquid batteries in pouches no longer exist, and the high ductility of aluminum plastic film can better adapt to the overall expansion and contraction formed during the migration of lithium ions, making its application prospects in all-solid-state batteries more promising. In the packaging process, solid-state batteries can omit the filling step, and the formation time can also be greatly shortened.
IV. Progress in the Industrialization of Solid-State Batteries
Semi-solid batteries: the first to be commercialized as a transitional solution
The commercialization of semi-solid batteries has a high visibility, and domestic companies are leading in layout. The path to the commercial application of solid-state batteries faces two major obstacles: technology and cost. The industry generally believes that the industrialization time node is around 2030. However, semi-solid batteries still retain the separator and some electrolyte, the material system changes less compared to liquid batteries, and the process equipment has a high overlap with liquid batteries, which can inherit the existing mature industry chain and is expected to achieve industrialization first. Therefore, many domestic companies choose semi-solid batteries as a transitional stage product, actively carrying out research and development and capacity layout, including representative companies such as WeLan New Energy, QingTao Energy, Ganfeng Lithium, and HuiNeng Technology. Currently, the highest energy density of semi-solid batteries that have passed vehicle verification can reach 368 Wh/kg, which is about 40% higher than mature high-nickel ternary batteries. According to our statistics, as of the end of 2023, the total capacity planning of semi-solid batteries publicly announced in China has reached 240GWh.The era of semi-solid-state battery vehicle loading has arrived, accelerating the pace of industrialization.
On January 9, 2021, NIO unveiled a 150kWh semi-solid-state battery pack at NIO Day, marking the beginning of frequent good news about the progress of semi-solid-state automotive-grade batteries. Driven by the joint efforts of automotive companies and battery manufacturers, semi-solid-state batteries have gradually achieved mass production and vehicle loading delivery since 2022. For instance, WeLan New Energy, a supplier of semi-solid-state batteries for NIO, achieved battery pack production and vehicle loading delivery in November 2022 and June 2023, respectively. Data released by the Power Battery Alliance shows that in 2023, solid-liquid hybrid batteries from companies such as WeLan New Energy and Ganfeng Lithium achieved mass vehicle loading, with an installation volume of about 0.8GWh. Among them, WeLan New Energy's vehicle loading volume in November and December was 0.41GWh and 0.35GWh, respectively, indicating a significant acceleration in the industrialization process of semi-solid-state batteries.
Semi-solid-state batteries may lead to an increase in high-nickel ternary and silicon-based anode materials, as well as an increase in the added value of separators.
Compared to liquid batteries, semi-solid-state batteries reduce the amount of liquid electrolyte and increase the composite electrolyte of oxides and polymers. The oxides are mainly added in the form of separator coating and positive and negative electrode coating, while the polymers fill in the form of a framework network. There is a trend towards the iteration of high-performance materials for the positive and negative electrodes, so the demand for high-nickel ternary and silicon-based anode materials is expected to grow. DangSheng Technology has successively obtained orders for 25,000 tons and 30,000 tons of solid-state lithium battery cathode materials from WeLan New Energy and QingTao Energy, respectively, which the company disclosed as ultra-high nickel ternary materials. RongBai Technology, also a supplier of cathode materials for WeLan New Energy, provides products for the ET7 model equipped with semi-solid-state batteries, which are Ni90 high-nickel ternary. According to the environmental assessment of WeLan Huzhou project, the anode adopts a scheme of silicon-based materials doped with graphite. The separator is still retained and coated with a solid-state electrolyte coating, and the lithium salt is upgraded from LiPF6 to LITFSI, which will respectively increase the value of the separator and electrolyte lithium salt. En捷 Corporation, together with Beijing WeLan and Tianmu Pioneer, has established Jiangsu Sanhe, a company focusing on the research and development and production of semi-solid-state battery separators, which has achieved mass production supply to WeLan New Energy.
Automotive company plans provide ample room for the large-scale application of solid-state batteries.
The advantages of solid-state lithium batteries in energy density and safety have led major vehicle manufacturers to accelerate the adoption of solid-state batteries, considering them as the main technological route for the next generation of power batteries. International vehicle manufacturers, including Toyota, Nissan, BMW, and Ford, all plan to launch electric vehicle models equipped with all-solid-state batteries between 2025 and 2030.
The industrialization conditions for all-solid-state batteries are not yet mature, and many difficulties still need to be solved jointly by the academic and industrial communities. Against this backdrop, vehicle manufacturers, research institutions, and battery companies, including startups, are actively committed to the development and mass production technology of the next generation of all-solid-state batteries. Currently, companies and institutions involved in the development of solid-state batteries are mainly concentrated in countries such as China, the United States, Japan, and South Korea. Japan: Vehicle manufacturers lead, with the earliest research and development layout, and lead globally in technology and patents.
Toyota is one of the pioneers in the global solid-state battery field, with leading patent layout. In 2019, it cooperated with Panasonic, and in 2021, they jointly launched a prototype car equipped with solid-state batteries. In October 2023, they announced a cooperation with Japan's Idemitsu Kosan Petroleum Company to conquer the mass production technology of solid-state electrolytes, striving to make all-solid-state batteries practical by 2027 to 2028. In terms of technology route, Japanese companies generally bet on the sulfide electrolyte with the highest conductivity, and small cylindrical batteries applied in the consumer electronics field have already achieved mass shipment.
South Korea still focuses on the three major battery factories, with independent research and development and external cooperation running in parallel.
South Korean companies' layout in the field of solid-state batteries is still concentrated on the three major battery companies: LG, SK On, and Samsung SDI. In November 2018, the three battery factories established a joint fund to jointly develop the core technology of the next generation of batteries, including solid-state batteries. Looking at the latest progress, Samsung SDI's commercialization schedule is the most advanced, planning to achieve mass production in 2027; SK cooperates with Solid Power in the field of sulfide electrolytes and also has research and development layout in the oxide route, with the research and development of polymer oxide and sulfide solid-state batteries expected to achieve commercialization in 2028; LG is currently still considering a semi-solid transition plan.U.S. Startups Full-Route Layout, Frequently Invested in by Car Companies.
The United States has a relatively shallow foundation in the field of traditional lithium-ion batteries, while a large number of startups have emerged in the direction of solid-state batteries, aiming to overtake in technological innovation. International car companies tend to choose to invest in such enterprises to layout the next generation of battery technology, such as Solid Power receiving investment from BMW, Ford, and Hyundai, and Quantum Scape has a deeper tie with Volkswagen. The technical route choices of various companies are quite diverse, covering all three types of electrolytes.
Domestic enterprises relying on university research achievements are leading the way, while traditional battery factories mainly focus on technical reserves.
Domestic enterprises leading the solid-state battery industrialization are mainly new enterprises with a background in university research, with typical representatives including Qingtao Energy founded by the team of Academician Nan Ce Wen from Tsinghua University, and Weilan New Energy established with the support of the Institute of Physics of the Chinese Academy of Sciences. At the same time, domestic car companies are also actively cooperating with these new enterprises to promote vehicle verification and production line construction. Traditional battery factories have more technical reserves and patent layouts in the field of solid-state batteries, but they are relatively conservative in promoting industrialization. Solid-state electrolytes are the core increment of the supply chain, focusing on research and development progress and supply situation.
As a key component of solid-state batteries, solid-state electrolytes have also received key layout from companies in the industry. In addition to solid-state battery companies developing and producing on their own, the leading companies mainly include Tianmu Pioneer and Blue Solid New Energy, both of which have mature products and production capacity at the level of thousands of tons. Both have a technical background from the Institute of Physics of the Chinese Academy of Sciences, just like Weilan New Energy. Shanghai Xi Ba and Jin Long Yu may hope to promote the mass production of related products through deep technical cooperation with the Shanghai Institute of Silicate Materials of the Chinese Academy of Sciences and Chongqing University, respectively. The solid-state electrolyte products of other companies are basically still in the laboratory research and development stage.
In the upstream resource end, electrolytes are expected to bring an increase in demand for minor metals such as zirconium, germanium, and lanthanum.
Oxide electrolyte LLZO uses zirconium dioxide as raw material. The domestic zirconium resource reserves are low and the consumption is large. The main downstream application fields are ceramics and refractory materials. Zirconium oxide suppliers include Dongfang Zirconium Industry, Sanxiang New Materials, and Kai Sheng Technology. A variety of oxide and sulfide electrolytes contain metal germanium, and the application fields of germanium are extensive, including optical fibers, infrared, photovoltaics, etc. China is a major country of germanium ore resources, and the main suppliers include Chihong Zinc Germanium and Yunnan Germanium Industry. Oxide electrolytes LLZO and LLTO also involve the use of lanthanum, which is a rare earth metal, and domestic contributions account for most of the global rare earth production.
Solid-state batteries mostly adopt the pouch route, which may increase the demand for aluminum plastic film.
Pouch batteries, with advantages such as lamination process, high energy density, and gel-state encapsulation technology, are expected to develop and apply in the field of solid-state batteries. Aluminum plastic film is the main packaging material for pouch batteries. Due to the high difficulty of production technology, there are strict requirements in aspects such as barrier performance, deep drawing, puncture resistance, resistance to electrolyte and insulation. The difficulty of controlling product consistency after mass production is also relatively large, making aluminum plastic film the only key material that has not yet achieved mass domestic production for pouch batteries at this stage.
At present, domestic companies with the ability to supply aluminum plastic film in batches mainly include Xinlun New Materials, Zijiang New Materials, Daoming Optics, and Mingguan New Materials.Please provide the text you would like translated into English.
Comments