A complete and detailed custom metal stamping manual-the ultimate guide to metal
2024-03-26
Metal Stamping - Overview
If you are in the manufacturing process and require metal components, then these metal parts should conform to the shape and design that you need. This is where the element of metal stamping comes into play.
Metal stamping ensures that you get the desired metal shapes.
Customers might wonder, what if I can't manufacture metal? You need not worry. Call a top metal stamping company, and they will handle the job for you.
However, even if you opt for outsourcing services, you must understand the process. This is why this article will discuss all the information you need to know about metal stamping.
What is Metal Stamping?
Metal stamping is a process used to transform flat metal sheets into specific shapes.
This complex process involves a series of metal forming methods such as stamping, blanking, cutting, punching, and bending, among others.
These cold forming methods use stamping presses and dies to ensure that the metal sheets are shaped according to the required specifications.In metal stamping, commonly used metals include titanium, zinc, aluminum, and nickel.
This process requires a significant amount of force (from 16 to 500 tons or even more), which necessitates the use of special equipment.
Advertisement
The equipment installed on the stamping press is called a die. It allows the metal to come into contact with the processing tools, thereby forming high-precision parts.
Modern Metal Stamping
Metal stamping has been around since the 7th century BC when the Lydians of Turkey used a basic form of metal stamping to produce coins.
Since the discovery of metals, many efforts have been made to enhance their utility, making metal forging a highly valuable profession.
Although metal stamping can be traced back to the 7th century, it later became important in the production of weapons, which required the manufacturing of many identical products.
In the 19th century, the positive development of stamping production led to the creation of household goods, thus necessitating mass production.
The Industrial Revolution accelerated the development of high-tech metal stamping equipment, as manufacturers needed to produce products in large quantities to meet market demands. It was not feasible to rely solely on forging and casting to accomplish the tasks.With the emergence of the automotive and shipbuilding industries, metal stamping has played a significant role in modern times. Metal stamping has made it possible to produce large-sized products.
Types of Metal Stamping
There are various types of metal stamping processes, including progressive die stamping, transfer die stamping, four-slide stamping, fine blanking, deep drawing stamping, and short stroke stamping.
Let's briefly understand each type of metal stamping.
Progressive Die Stamping
Progressive die stamping is a sequential stamping method. It has several stations, with each stage assigned a function.
Cutting, bending, and stamping have continuous stages.
After the metal sheet has gone through all the sequences, it will take on the required shape and size.Progressive stamping is suitable for manufacturing a large quantity of parts according to strict specifications and tolerances. This method involves feeding a coil of metal into stamping equipment, which then sequentially punches, bends, and forms the parts. The workpiece remains attached to the base strip from start to finish. Separating the finished parts from the metal strip is the final step of the operation.
The benefits of progressive stamping include:
- Short preparation time
- Reduced labor costs
- Rapid production
- Long-term
- Minimal waste
In short, progressive stamping can reproduce parts with complex geometries quickly and economically in a repetitive manner.
However, progressive stamping requires an investment in permanent steel tools.It is also not suitable for parts that require deep drawing. Progressive stamping can use different metals, such as steel, aluminum, copper, stainless steel, and brass as the main materials. Precious metal superalloys, titanium, and chromium-nickel iron alloys can also be used. In some cases, metal parts can be progressively stamped.
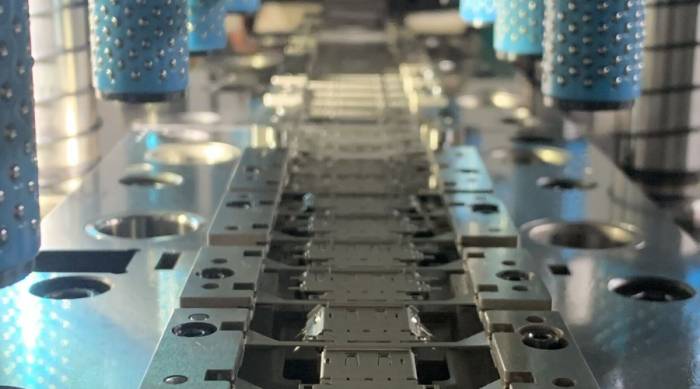
The method used in continuous stamping is accomplished by using transfer presses. These presses use fingers to transfer components from one place to another. For the production of large quantities of stampings that require complex press processes, progressive presses are recommended. One advantage of this type of press is the duration of the cycle. Depending on the component, production can easily exceed 800 parts per minute. However, this type of press is not suitable for high-precision deep drawing, as your stamping depth may be greater than the size of the part/component.
The process is carried out with the help of transfer presses. It operates at a slower speed, using mechanical fingers to hold the parts in place throughout the entire forming or shaping process. Progressive presses are just a small part of the forming process controlled by sleeves using springs or similar devices. It can lead to issues such as uneven material thickness.Compared to transfer presses, another disadvantage of progressive presses is that they require a greater amount of raw material for the transfer components. These tools are more costly because they are built-in modules. They do not have specific provisions tailored for each station. Moreover, they are incapable of performing processes that require the component to leave the strip, such as hemming, necking thread rolling, hemming flanges, rotary stamping, and so on. The number of functions determines the required cost and tools. It is recommended to keep the tools as basic as possible to minimize tooling costs. Features that are too close together can cause issues because they may not provide adequate punching space, which often leads to the need for a second station. There may also be problems with protrusions and narrow cuts. Dies are typically made of tool steel, which can withstand high impact loads, maintain the required sharp edges, and resist wear.
Progressive Die StampingTransfer die stamping machines treat each part as a whole, hence the first step in the stamping sequence is to separate the part from the metal strip. Then it is transported by hand to various stations that perform individual operations.
The most laborious task in creating a process sequence is determining the number of required forming stations, tool geometry, overall dimensions, tolerances, residual stresses, and surface finish that meets the product requirements.
Transfer die stamping process is similar to progressive stamping because it uses sequential processing.
The main difference is that the stamping part is separated from the metal strip at an earlier stage in the process. This process is best suited for large metal parts and/or parts with complex design elements (such as pipes/tubing, grooves, ribs, and threads).
It can also be used for manufacturing deep-drawn parts because there are no connecting metal strips on the part. The press can stamp within the limits allowed by the raw material.
Commonly used materials include aluminum, brass, copper, stainless steel, and precious metals, but parts can also be made from ferrous and non-ferrous materials.
Fourslide stamping is a complex metalworking process that combines stamping and forming, capable of manufacturing small, intricate parts/components from wire or metal coils.
Compared to traditional pressing methods, this approach offers several advantages, including increased flexibility and design versatility, improved speed, and reduced production costs.Leveraging these advantages, four-slide stamping has become the preferred manufacturing method for high-precision products and applications across numerous industries, ranging from automotive to aerospace, and extending to medical and electronics sectors.
Metal stamping, which is the opposite of the vertical movement of a stamping press, is performed by four-slide metal stamping machines that use four moving slides to execute the stamping or forming process at right angles.
Four-slide stamping is akin to multi-slide stamping. However, multi-slide stamping machines offer more functionality than just four slides.
Four axes are connected to a series of bevel gears and are driven by a single motor that propels the slides.
Camshafts attached to each axis handle the slides, which strike the metal workpiece in four orthogonal directions as it is fed through the machine.
This multi-directional approach allows for the simultaneous or sequential bending or stamping of the workpiece from all four sides.
A single four-slide operation can produce complex shapes using a multitude of curves, bends, or twists.
Precision Stamping
Precision stamping, also known as fine blanking or precision blanking, is a process that aims to manufacture parts with clean, smooth surfaces.
The primary goal of precision stamping is to create components that exhibit high levels of dimensional accuracy and surface finish, which are essential for applications where close tolerances and aesthetic quality are paramount.The difference between fine blanking and standard blanking lies in the fact that the material is sheared during the blanking process only. There is no rupture after all sides are clamped.
In fine blanking, there is no rapid passage of force. Therefore, it is quieter and has less vibration.
The cost of tools is higher than the cost of traditional blanking, and the process cannot be carried out at extremely high speeds.
Deep Drawing Stamping
The deep drawing stamping process shapes flat metal into a mold to create precise, often cylindrical parts.
It is achieved by feeding a flat metal coil into a press, which is then surrounded by a tool station. Each station repeats a process on the steel.
The deep drawing stamping process is used to stamp metal sheets into various hollow axisymmetric parts. The shapes created using this stamping method are cylindrical, but it can also create box-shaped objects.
Deep drawing stamping can be used to manufacture a variety of industrial and household items, such as sinks, baking pans, sanitary ware, automotive parts, beverage cans, casings, and so on.
This type of stamping applies pressure to the metal sheet with a punch, pulling it radially into the die cavity.
The metal sheet is first placed on the forming mold and secured in place at each end by the compressive force applied by the edge press.Secondly, by applying axial force to the metal sheet through mechanical stamping tools, the metal sheet is deformed and flows into the die cavity, forming the required shape.
The term "deep drawing" is so named because the depth of the component is greater than its diameter.
Short-term stamping
Short-term metal stamping is a process used for manufacturing a small number of perforated metal parts.
Short-term production can be defined as a run producing fewer than 5,000 parts (depending on the manufacturer).
Short-term metal stamping is applied across a wide range of industries. It is suitable for small batch seasonal products, special products, or situations where high investment in permanent tools is not feasible.
Metal stamping is cost-effective, versatile, quick to set up, and provides precise cutting and shaping.
Short-term metal stamping offers a cost-effective method for producing high-quality, reliable parts with faster turnaround times.
If you are looking for faster delivery speeds, short-term production may be a good option for you.Short-term production is applied across various industries, such as:
Automotive
Aerospace
Commercial lighting
Construction
Electronics
Home appliances
Medical
Short-term metal stamping processes can create uniform parts using metals like aluminum, brass, copper, and steel.Short-term stamping requires a small amount of material, thereby reducing manufacturing costs.
Metal Stamping Process — A Step-by-Step Procedure
After design and prototyping, a series of multiple steps are needed to create complex metal parts, assemblies, or components. This is a task much more challenging than most people imagine.
Parts that seem simple at first glance rarely require only one stamping step to be considered complete.
Confusion often arises when trying to determine the best metal stamping process.
When selecting a metal stamping process, it is necessary to consider,
• How will the process affect the design functionality?
• Design or industry-specific requirements?
• Production time and cost-effectiveness?Common Metal Stamping Processes
There are several metal stamping processes. They include blanking, piercing, drawing, bending, air bending, coining and embossing, forming, trimming, slitting, stretching, ironing, necking/reducing, and hemming.
Blanking
If necessary, the blanking process is the first step in your stamping method.
Blanking refers to the process of cutting large sheets or steel/metal coils into smaller, more manageable parts.
This process involves cutting a rough outline of the product shape you want to achieve at the end of the entire metal stamping process.
During blanking, the main focus includes the hole diameter, length, geometric shape, spacing, etc., in the blanking process.
Blanking not only allows you to visually understand what is expected. It also helps to minimize the amount of waste that may occur later.
It also eliminates the issue of wasted time. Trimming usually occurs when metal objects are drawn or formed.Punching
If the parts you are processing require holes, slots, or other notches, you can use the punching option.
Punching is done simultaneously with blanking, which can form the desired shape from a metal sheet or plate.
Drawing
Drawing is the actual stamping process.
The punch presses a portion of the metal into the die to form the basic shape of the part.
Parts with a depth less than the main opening are considered shallow drawing.
Parts with a depth higher than the opening are deep drawn.Bending
Bending is a process that is easy to understand. A workpiece is placed on a specially designed die, and a press head forces the metal into the desired bend.
Bending is performed after stretching because the metal part that is bent in stamping will cause the entire part to deform.
Air Bending
Air bending refers to the process of bending the flat part into a die (usually V-shaped) with a punch. The distance between the punch and the die is greater than the thickness of the metal, resulting in a slightly relaxed bend when the part is removed. Compared to most other bending techniques, air bending is less energy-intensive in terms of pressure and power.
Bottoming and CastingLaying and embossing are two bending methods similar to air bending, but the pressure used is 2 to 30 times the pressure.
The material is pressed into closely fitting dies, resulting in a more permanent bend.
Forming
Forming is a bending process similar to laying, bending, and embossing. It is used to manufacture parts with multiple bends in one step, such as U-shaped bends.
Shearing
Shearing involves cutting metal sheet fragments and separating them as scrap metal. This is a novel method because the metal is squeezed in a vertical plane.
It is commonly (but not always) used for cutting out deep-drawn cups from sheets.A unique process, bloodletting is used to create labels or vents.
A piece of material is cut with three edges while being bent.
This method creates openings or hook-like designs. The removal of waste material is a secondary processing step.
The stamping process involves various techniques, but not every method is effective or even necessary for every component.
When you fully understand the process, you can create parts that can reduce waste, lower costs, and speed up production without sacrificing quality.
Stretching
Here, we increase the surface area of the metal sheet. To achieve this, tension is added while minimizing the inward movement of the edges. This process also helps to smooth out metal parts.
Ironing
The metal sheet is compressed to minimize its thickness. Ironing is crucial in applications such as the manufacturing of beverage cans.Reducing Neck or Reducing Diameter
A reducing neck machine or reducing diameter machine is designed to decrease the diameter of a tube.
Flanging
During the flanging process, the edges of a metal sheet are folded to make them thicker, which increases the strength and stability of the shape.
Custom Metal Stamping
Custom metal stamping is the process of forming metal, requiring custom tools and techniques to manufacture parts. Various applications and industries adopt custom-designed stamping processes to meet mass production needs and ensure that each part conforms to precise specifications. Custom-designed sheet metal stamping can include operations such as blanking, cutting, stamping, and drawing with embossing.Each step is completed with tools designed using CAD/CAM software, which provides the precision required for complex parts.
Sheet metal stamping is an efficient and effective method for manufacturing high-quality, durable parts for various industries, including hardware, electronics, medical, aerospace, industrial lighting, and more.
Fine machining operations in hardware stamping
When creating and manufacturing precision hardware stampings, engineers and project managers from manufacturing companies, along with their suppliers and hardware molds, need to discuss fine machining options to ensure optimal performance.
In most cases, the final product of the hardware stamping process may not be ready for use. Some fine machining operations may be required to perfect it.
The most common post-stampings include tapping, cutting, reaming, and deburring. These finishing processes improve the appearance of the product and make it compatible with other machinery.
Deburring removes the residual metal material left after the stamping process. It removes sharp burrs and ensures that all metal parts are smooth.
Metal surface treatment and this key element in the manufacturing process, which is necessary to prevent corrosion, improve appearance, or smooth sharp edges, should be considered from the outset.
Finishing options includePowder Coatings and Electronic Coatings
Electroplating
Electropolishing
Debur
Heat Treatment
Cleaning
Metal Stamping Materials
Precision metal stamping machines can produce high-quality parts, but choosing the right raw materials is also important, just like choosing the right processing procedures.
Each alloy and metal has unique characteristics. Based on the composition, one can select common alloys or special metals.Various common alloys are used in metal stamping and are precisely designed across various industries. They include:
Aluminum alloys
Brass alloys
Copper alloys
Nickel alloys
Steel and stainless steel.
Engineers and designers must have a basic understanding of the most commonly used metals and special metals to assist in material selection.
Benefits of Metal Stamping
Metal stamping is a well-known manufacturing process because it offers many advantages.Batch Production: Encourages the mass production of products and parts.
High Precision: If a metal sheet is cut or bent, the outcome will be accurate parts/components obtained through proper measurements. Modern metal stamping equipment is designed to operate with high precision.
Uniformity: In mass-produced products, stamped parts ensure that each part remains uniform, with each part's shape, design, and dimensions matching the specifications exactly.
Cost-Effective: Metal stamping is a cost-effective manufacturing method. By using metal stamping, manufacturing enterprises can produce products quickly and efficiently.
Time-Saving: Outsourcing the metal stamping process can spare you from all the hassle, saving you time and allowing you to devote your skills and energy to other projects.
General Information: It is classified as a cold working process, and like other cold working methods, it does not alter the properties of the metal due to heat-related changes.
Metal stamping does not expose parts to extreme temperatures, thus eliminating the risk of changes due to heat. Metal parts can be formed through stamping without the need for heating.
The effectiveness of metal stamping makes it the preferred choice for large manufacturing companies.
Selecting the Best Metal Stamping CompanyBefore selecting a reliable metal stamping manufacturer, there are many factors to consider.
Expertise and Experience: Metal stamping uses specialized equipment to form patterns ranging from simple to complex. It begins with flat metal sheets that can be shaped and/or pierced. You need to check the manufacturer's level of experience to ensure they can proficiently produce the parts you require.
Cost-effectiveness: The cost of a project is a function of quantity. The cost per piece is higher for small batch production compared to mass production. This is why we encourage the production of bulk parts to take advantage of economies of scale.
While cost is certainly a consideration, it is not the only factor to take into account once a company's reputation, capabilities, and knowledge have been confirmed.
Company Reputation
Assessing the reputation of the metal stamping manufacturer under consideration should not be difficult.
Most Original Equipment Manufacturers (OEMs) will choose stamping companies that are close to major transportation routes and their main business locations to reduce supply chain issues and make logistics easier to manage.
Check for timely delivery of business orders, ensure the company is registered with ISO 9001, and look for companies that are members of the PMA (Precision Metalforming Association).
Industry Experience
**Industry experience is crucial when it comes to selecting a metal stamping manufacturer. A manufacturer with extensive experience in the industry will have a deep understanding of the latest technologies, materials, and processes involved in metal stamping. This experience can translate into higher quality products, more efficient production, and better problem-solving capabilities when challenges arise.**
**When evaluating a manufacturer's industry experience, consider the following:**
1. **Years in Business:** How long has the company been in operation? A longer track record often indicates stability and a proven ability to adapt to industry changes.
2. **Diverse Portfolio:** Has the manufacturer worked with a variety of clients and industries? A diverse portfolio can be a sign of flexibility and the ability to handle different types of projects.
3. **Innovation and R&D:** Is the manufacturer committed to research and development? Continuous innovation is key to staying competitive and offering cutting-edge solutions.
4. **Certifications and Standards:** Are they certified to industry standards such as ISO 9001 for quality management? Certifications can provide assurance of a manufacturer's commitment to quality and compliance.
5. **Customer Testimonials and References:** Can they provide testimonials or references from satisfied customers? Hearing from others who have worked with the manufacturer can provide valuable insights into their performance and reliability.
**By considering these aspects of industry experience, you can make a more informed decision when choosing a metal stamping manufacturer that will meet your specific needs and expectations.**In addition to the company name, it is also important to ensure that the stamping company you are considering has verified expertise in your field. Many leading manufacturers have decades of experience in providing parts for the aerospace, automotive, HVAC, metal structure, and building materials industries, as well as developing and supplying special parts and components for these sectors.
Production Capacity
Production capacity is influenced by lead times and the equipment used. Modern facilities utilize the most advanced precision equipment to complete projects according to exact specifications, with tight tolerances that cannot be achieved with older equipment and systems.
Determining the Cost of a Metal Stamping Project
Stamping tools, also known as "hard tools," can be very expensive. For small quantities (fewer than 10,000 pieces), the cost of hard tools outweighs any possible return, making "metal spinning" a viable alternative. Spinning tools are not expensive. Spinning tools are typically 10 to 20 times cheaper than stamping tools.
Cost is a major consideration, but time is also very important. In addition to being costly, the delivery time for stamping machines is also longer. Spinning tools and parts can be completed in just a few weeks, rather than months.Metal Stamping Applications
Metal stamping has a broad range of industrial applications. Industries that require 3D design typically utilize metal stamping.
Once you have completed the 3D design of your product, metal stamping machines will consistently produce and reproduce parts in large quantities.
Industries that use metal stamping companies include (but are not limited to),
Automotive
Industrial machinery
Consumer electronics
Aerospace
ElectricalTelecommunications
According to data from Grand View Research, the automotive industry is a major market for the metal stamping industry, accounting for 34.7% of its revenue in 2016.
However, in this technological era, the application of metal manufacturing in the consumer electronics sector is flourishing.
This means that almost all businesses that use consumer electronic devices in the workplace rely on products manufactured by metal stamping machines.
Smaller industries that manufacture household appliances and jewelry can use stamping machines for larger-scale production of their products.
Dongguan Gaolv: Your Reliable Metal Stamping Company
Our Company:
Dongguan Gaolv offers customized metal stamping, manufacturing, and production at reasonable prices.
Our Guarantee:From the initial prototype design phase to the final product, we will complete your order within four weeks.
Dongguan Gao Lue is an industry leader in custom metal stamping and manufacturing. From rigorous prototype design to the final product, we handle all work in-house. This provides us with the ability to offer higher precision, greater efficiency, and the capacity to provide impressive cost advantages.
Our experienced team utilizes cutting-edge technology to achieve the highest quality and a fast delivery of 4 weeks. All of this brings considerable savings and new market opportunities to your business at a competitive price.
Dongguan Gao Lue excels in custom metal stamping for parts. Since 1999, we have provided countless customers with the innovation, improved efficiency, and strict quality parts needed to drive business growth.
Our goal is to ensure your experience is smooth and painless. Professional designers and technicians use the latest technology and manufacturing techniques to turn your vision into an exciting reality. You can benefit from our expertise and decades of experience.
We provide custom metal stamping and related services for consumer electronics, new energy vehicles, industrial automation, medical, aerospace, communication, and other fields.
Using Dongguan Gao Lue is easy. Choose your materials, dimensions, and tolerances. Share your requirements, including drawings. Unsure about your product specifications? Send us your information in CAD, 3D drawings, or photos. Our team can typically take it from there.
Once the product details are determined and key components are selected, we work closely with your technical team to ensure rapid procurement of materials and components to meet our accelerated production schedule.
With Dongguan Gao Lue, your products can enter the market faster, creating new opportunities for your sales team. You enjoy increased revenue to boost your bottom line. We reap the greatest rewards as you transform your industry with the latest innovations. Please contact Dongguan Gao Lue to discuss your metal stamping and manufacturing needs. Our team can quickly turn your ideas from concept to completion at a cost that fits your budget. Dongguan Gao Lue is committed to being the best. Proudly manufactured in China.
Comments