8 common surface treatment methods for metal stamping parts
2024-03-22
It may sound like a cliché, but indeed, prevention is better than cure. This is true for any manufacturing, especially in the metal stamping industry. Metals are subject to wear, corrosion, environmental hazards, and more. The various processes involved in stamping help to minimize these potential metal failures—one of which is metal surface treatment or metal finishing, which can provide further protection for the metal.
Understanding its application on metals (depending on its corrosiveness, potential exposure, etc.) is beneficial and essential for us. In the long run, surface treatment can save us more money and less production time. This article will delve into the importance, advantages, and common types of metal surface treatment.
What is Metal Surface Treatment?
Metal surface treatment is the creation and application of a layer or physical barrier to protect the metal before the coating occurs. This process includes metal cleaning, deburring, polishing, etc. It not only increases the structural integrity of the metal but also enhances these parts or components aesthetically.
However, when it comes to metal surface treatment, there are some factors to consider—such as production speed, cost-effectiveness, and metal durability. You must ensure that everything aligns with the company's goals and the application of the metal parts. This is why careful planning from the metal stamping production to surface treatment is recommended.
Advertisement
To continue your learning, here are the steps for metal surface treatment:
Firstly, you need to clean the surface from stamping compounds and grinding oils.
Then, apply an organic or inorganic sealant.
Rinse with deionized water.Finally, to remove moisture, you can place it in an oven or air dry.
Why is surface treatment of metals necessary?
The production and design of precision metal stampings are of paramount importance. Therefore, planning surface treatment options is essential. This process increases the lifespan of metals—making them more significant in the use of other industries. Moreover, it can expand your company because you know you are providing high-quality stampings.
In addition to the above statements, there are many reasons why we should treat metal surfaces, all of which are worth understanding:
Corrosion inhibition—A rust-free metal is a good sign of a reliable material suitable for any application. Stampings must have high corrosion resistance to galvanic corrosion, pitting, and crevice corrosion.
Improving appearance—Surface treatment makes metals more pleasing and aesthetically balanced for decorative purposes. It can be matte or shiny, embossed or plain, etc.
Enhancing durability—As mentioned earlier, it can extend the lifespan of metals. It can harden the surface of parts, which is very needed in the production of stampings for medical equipment, building materials, and automotive parts.
Enhancing electrical performance, colorfastness, and chemical resistance—These benefits provide an impeccable advantage in increasing the value of metals.
Which industries use metal surface treatment?
Almost everything we see, use, and build is the result of surface treatment of hardware stampings that are components of entire devices. Industries such as industrial electronics, medical, industrial, aerospace, communications, and other companies utilize this process to improve their tools, items, and equipment.For instance, in the electronics industry, we utilize it for covers, connectors, sensors, shelving, and more, which you can find in mobile phones, computers, and appliances. In the medical field, we perform surface treatments on stamped parts for laboratory equipment, such as device pumps, monitors, surgical equipment, and so on.
This list goes on, as our current era primarily relies on services, processes, and metal stamping to produce customized, high-quality metal components.
Material and Related Finish Selection
Now that we have delved into the importance and advantages of metal surface treatments, it is time for you to consider the appropriate method for the right materials.
As is well-known, different materials and products require different surface treatments. We have a wide array of types, but the list below will show you eight (8) common metal surface treatments for stamped parts that typically yield high-quality results:
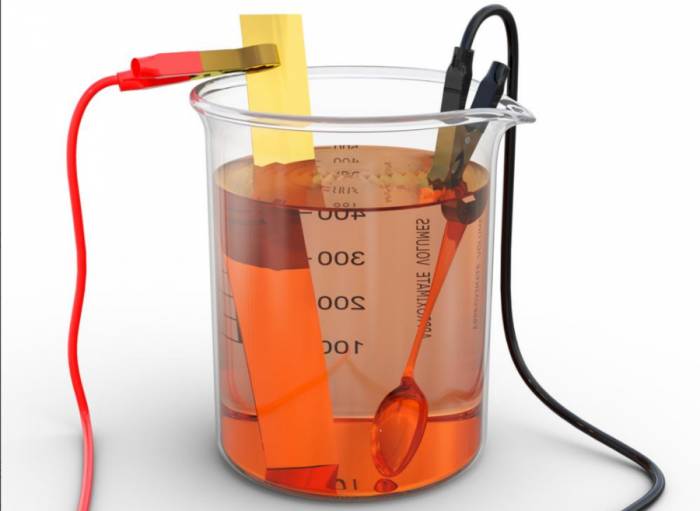
Electroplating
Electroplating is a chemical process that involves the application of a thin metal coating onto the primary metal surface using an electric current. Due to its versatility—from miniature parts to large-scale products—this method is a widely used surface treatment technique. It aims to protect metals from corrosion, enhance surface value, and amplify their physical appearance.
Laboratory and medical equipment, household appliances, and automotive metal parts all employ this treatment method. Moreover, electroplating is primarily suitable for a variety of metals, such as:
Standard metals (for example, copper, nickel, tin, zinc)Precious metals (such as gold, silver, palladium, rhodium)
Hard chrome and cadmium
Chemical plating
Contrary to electroplating, chemical plating is not carried out through an electric current. Instead, it uses chemical reactions to apply a metal coating onto the target metal (or what we refer to as the "substrate"). Its application is smoother and more uniform than electroplating. It is also more cost-effective throughout the entire process.
The metal used for this type of surface treatment is nickel. These products provide the majority of components for industries such as the aerospace industry and firearm manufacturers, among others. Chemical plating is also beneficial for stamping metal parts, such as:
Aluminum
Steel
Copper
Zinc
BrassChemical Coating
This type of surface treatment, also known as powder coating, involves the application of a smooth protective film onto the substrate using compressed air, which then melts the powder material. It provides stamped metals with a high degree of scratch and crack resistance, corrosion resistance, and is valuable as a metal colorant.
The automotive industry widely uses chemical coatings for its components, making it an ideal choice for customer preferences. Additionally, the materials used for this surface treatment are aluminum and steel.
Metal Anodizing
Anodizing is the electrolytic oxidation of the metal surface to form a protective film of oxide coating. It is highly suitable as a metal surface treatment to minimize wear and tear, resist corrosion, and make metal components more robust and intricate.
On the other hand, it is not suitable for stamped parts with rough and damaged surfaces because it can only coat evenly. It is limited to aluminum metal components.
Hot Dip Galvanizing
This surface treatment, also known as hot-dipping, involves coating stamped parts of steel and iron by immersing them in a molten zinc bath. Through this process, metal components are most likely to have a high degree of corrosion resistance. The hot-dipping method is popular in the industry for manufacturing consumer appliances and automotive metal parts.
Vacuum Metallization
Vacuum metallization is the process of applying a protective metal barrier to smooth out stamped parts. This type of surface treatment requires the metal to be placed inside a can or container where a metal coating is sprayed. It features a mirror-like finish suitable for decorative and design purposes, particularly in the aerospace and automotive industries. Aluminum is the key metal for this method.Painting
Coating has many applications, such as spray painting, electrostatic coating, conductive coating, lubricant coating, and so on. This type of surface treatment provides excellent corrosion and rust prevention capabilities, and enhances the appearance of any metal stamping parts.
Thermal Spraying
This surface treatment enhances the ability of metal parts to eliminate or minimize metal surface scratches, peeling, and cracking by melting and heating metal coatings. It serves as a primer for large structural metal stampings.
Metal Surface Treatment has a significant impact on metal stamping. It can enhance and add value to stampings in terms of durability, corrosion resistance, and aesthetics. In terms of quality, it benefits all manufacturers, suppliers, and customers. No wonder this method must be carefully planned.
However, please note that everyone must be aware of the factors to consider in metal surface treatment for stampings. To prevent unnecessary outcomes, you should review some matters, such as – the duration and work that needs to be done, your company and partners' goals, and the requirements needed for the product.
Always ensure that the precision of the metal stampings is not affected and that there is enough time to decide which type of surface treatment can add value to your products and establish your reputation. For your metal stamping needs, please visit us.
Comments