How to make the best choice between metal stamping and laser cutting
2024-03-10
Let's start by defining terms, which is the best way to ensure we're all on the same page.
What is metal stamping?
In a 30,000-foot view, metal stamping uses dies to shape/form the parts you want to create. During the metal stamping process, the die applies sufficient pressure to force the malleable metal into the shape of the die.
What is laser cutting?
Laser cutting is a completely different process that uses an extremely powerful, precisely guided laser to cut metal into the desired part shape.
What factors are involved in choosing one over the other? Four factors will inform your choice. They are,
Cost,
Material,Time,
Capability.
Let's examine each of the aforementioned factors in order.
Cost
Cost is almost always the biggest factor considered in any business decision, and the choice between metal stamping and laser cutting is no exception. The unique properties of laser cutting might lead one to think it is the most expensive option. However, other factors might prove this assumption to be incorrect.
For instance, metal stamping requires the fabrication of unique dies for the parts/components being stamped. This takes time, and for complex geometric shapes, it can even require more time and higher costs. The upfront costs can be substantial. In mass production, this expense might easily be justified, as the cost per part is relatively low. However, this may not be the case for small batch production.
Advertisement
For example, a small metal stamping run for parts with complex geometric shapes might incur a significant amount of part costs and longer lead times due to the complexity of the dies. In such cases, using a laser cutting machine might be a better choice from both a cost and lead time perspective.
It is important to consider all variables to make a reasonable decision.
MaterialsComponents can be made from any of a variety of materials. The material you choose will affect whether to use metal stamping or laser cutting. For our purposes, we assume that the material you select is chosen after careful consideration. We may discuss material selection in another article, but not here... not today.
Assuming you have a medium-scale production run using a very hard material, such as annealed and stress-relieved 430 stainless steel. As you know, forming this metal can cause tools and dies to wear out quickly, so maintenance and replacement costs must be a factor in your choice.
It is well known that metal stamping is accomplished through mechanical force, which can lead to micro-fractures and/or stress marks. Sometimes this is unacceptable for components. However, laser cutting does not use mechanical force and does not produce stress marks or fractures.
Material waste is another important consideration when deciding between metal stamping and laser cutting. For instance, when cutting shapes from a sheet of metal, the laser cutting method allows for closer cuts between shapes than stamping. This important quality in laser cutting can significantly reduce waste.
Finish is another consideration in making a choice. Materials stamped may have burrs or sharp edges that require further processing to address. In contrast, laser cutting does not leave sharp or burrs.
Time
While time and cost are not interchangeable, they share many similarities, as time is money!
When you assess the pros and cons of one method over another, time is a key factor. For example, when you are racing against the clock, choosing the laser cutting option can significantly reduce lead times.
As mentioned earlier, using laser cutting can also save time because the method does not leave burrs or sharp edges, meaning that the finishing time is reduced to zero.Using the laser cutting option can reduce maintenance and downtime. As we mentioned earlier, molds and tools wear out, necessitating ongoing maintenance. Lasers do not wear out. This is a significant factor, especially when manufacturing components with very hard metals.
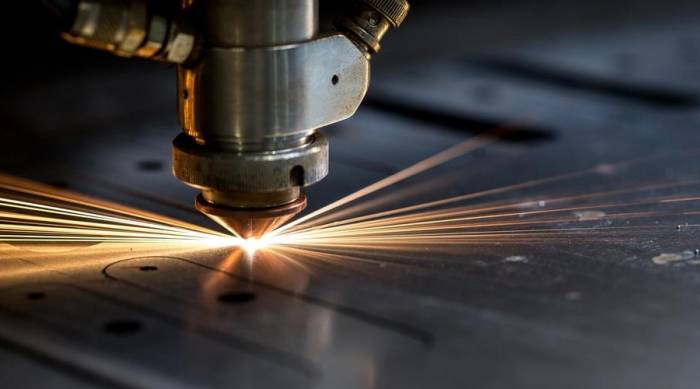
Capabilities
The capabilities of laser cutting and metal stamping can be best displayed using a Venn diagram. In the example below, "A" represents laser cutting, "B" represents metal stamping, and "AB" represents the overlap of their capabilities.
The above illustration explains why a choice must be made, as in each case, neither method is the optimal solution. More importantly, even if either method could achieve the desired effect, you must consider the prudence of using a cannon to kill a mosquito, which a fly swatter can also do.
There are things that lasers cannot do, such as bending! If your parts require bending, laser cutting is not a viable solution. On the other hand, metal stamping can flatten, forge, and cast metal. Adding a bending machine also allows for bending. However, it should be noted that bending can create structural weaknesses, especially when bending exceeds the limit of the metal's inner radius, or if some improper movement occurs during the process, the metal may become brittle and prone to breaking.
Laser cutting limits the thickness of the material being cut. This limitation may come from the hardness or thickness of the material. If it exceeds the parameters of the laser, it may lead to chipping and/or deformation.
Due to the high temperatures involved in laser cutting, the physical properties of certain metals/alloys may change, which could affect the performance of the part. When you use metal stamping, this is not an issue, as force rather than heat is used to cut the material.
The combination of a metal stamping press (press brake) with a bending machine is a versatile manufacturing process capable of forming complex shapes, including precise bends at various angles. Complex geometric shapes, especially those that include bends, are best addressed using this tried-and-true equipment.Making Decisions
I believe that after reading this article, you will understand the importance of considering all aspects of manufacturing parts/components. Many variables must be taken into account, such as the metal/alloy used, the complexity of the part's geometry, whether it is bent or not, the target cost for each part, overall budget considerations, and so on.
The choice between laser cutting and traditional metal stamping is complex and requires careful consideration and a thorough understanding of your end goals. My aim is to at least provide you with a starting point for the thought process. Have I covered all contingencies—probably not? However, if you understand the interplay between the variables and factors involved in making a decision, then I have done my job.
Closing Thoughts
Before deciding between laser cutting and metal stamping, I encourage you to read about each process to thoroughly understand the cost, time, and functionality of each method, especially regarding the materials you plan to use.
Both methods are used daily in tens of thousands of manufacturing companies. In most cases, both methods can get the job done, but you should be aware that each method has its unique advantages and disadvantages.
The experts and experienced staff at Dongguan Gaolue are always ready to provide any help and guidance you may need, and we encourage you to get in touch with us. Our talented team is always ready to assist.
Comments